From the Cement plant ...
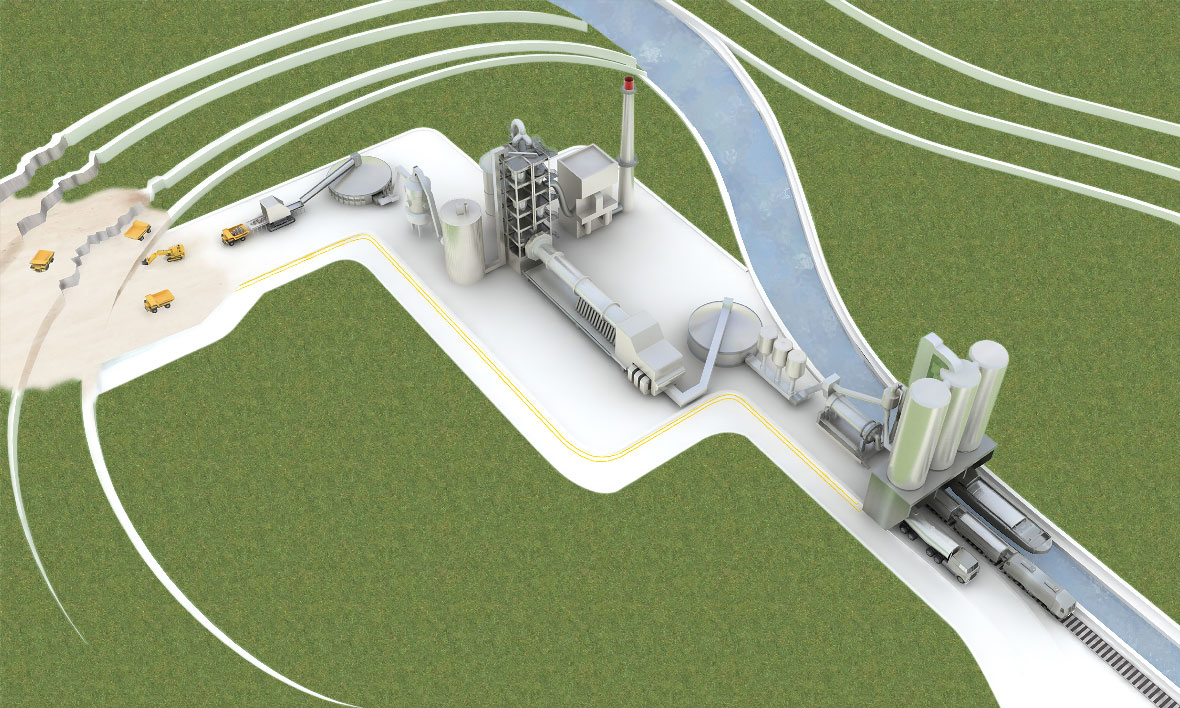

EXTRACTION OF RAW MATERIALS
Back

EXTRACTION OF RAW MATERIALS
The main raw materials required to manufacture traditional, Ordinary Portland Cement (OPC) are limestone and clay. Rocks are extracted from a quarry by blasting and then routed to the nearby cement plant on a conveyor belt.
Project Solid Life:
The main raw materials required to manufacture Solidia Cement™ are a source of CaO (e.g., limestone) and a source of SiO2 (e.g., clay or sand).






GRINDING AND STORAGE OF RAW MATERIALS
Back

GRINDING AND STORAGE OF RAW MATERIALS
The minerals from the quarry are routed to the grinding plant where they undergo initial milling before being reduced to a fine powder. The raw materials (80% limestone and 20% clay for OPC) are then stored in a pre-homogenization pile. This mixture is called « raw mix ».
Project Solid Life:
The ratio of the raw mix components used to produce Solidia Cement clinker is different than that used in traditional OPC. In particular, Solidia Cement has a lower limestone content, which is balanced by a higher clay or sand content.






THE FIRING OF RAW MATERIALS
Back

THE FIRING OF RAW MATERIALS
For the production of OPC, the raw mix is fed into a preheating tower and then enters a horizontal rotary kiln heated to approximately 900°C. The temperature is then raised to 1450°C. Combustion causes a chemical reaction called “decarbonation,” which releases the CO2 contained in the milestone. The fired materials take the form of hard granules called “clinker”.
Project Solid Life:
The lower proportion of limestone in the raw mix used to produce Solidia clinker results in a significant reduction of CO2 emissions. The clinker of Solidia Cement is produced at a temperature of about 1200°C, which is roughly 250°C lower than the sintering temperature used in OPC clinker manufacturing. The resulting process emits 30% less CO2.






STORAGE AND GRINDING OF CEMENT
Back

STORAGE AND GRINDING OF CEMENT
Following re-cooling, the clinker is stored in silos, then transformed into cement according to production requirements. During the final manufacturing stage, gypsum is added to the clinker, in a proportion of 3-5%, and the mixture is finely ground.
Project Solid Life:
Solidia Cement does not require any additional materials. Conventional cementitious materials can be added to further reduce the CO2 footprint of the cement.






PACKAGING AND SHIPMENT
Back

PACKAGING AND SHIPMENT
The cement is stored in silos before being
delivered in bulk using tanker trucks or
packaged into 25-35kg bags and stacked on
pallets. Various means of transport may be
used according to the local infrastructure
and topography.
Since the market for construction materials
is a local market, transportation distances
are relatively short.





... to the Precast plant
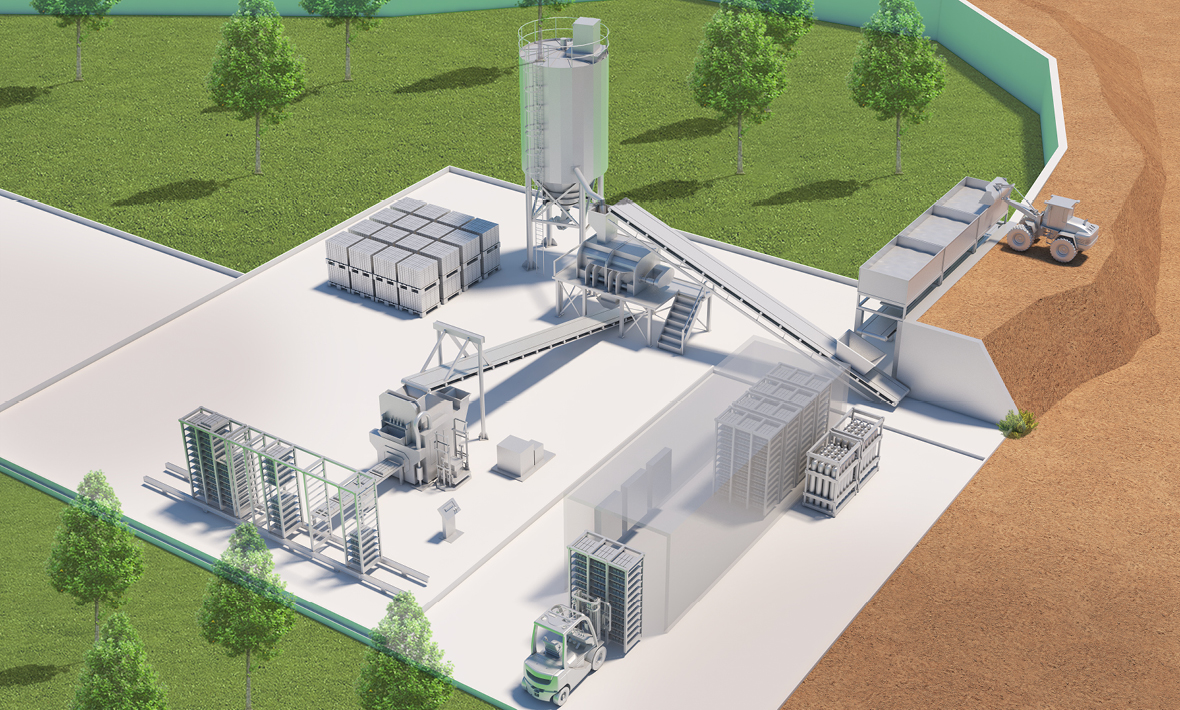

CEMENT STORAGE AT PRECAST PLANT
Back

CEMENT STORAGE AT PRECAST PLANT
At precast plant, the cement is stored in silos.
Project Solid Life:
A dedicated cement silo is needed for Solidia Cement storage. Solidia Cement only reacts with CO2, unlike OPC, which reacts with water.







PREPARATION OF RAW MATERIALS FOR CONCRETE
Back

PREPARATION OF RAW MATERIALS FOR CONCRETE
Concrete raw materials are fed into hoppers and added to the mixer.
Project Solid Life:
Solidia Concrete™ uses the same raw materials as OPC.







CEMENT AND RAW MATERIALS MIXING
Back

CEMENT AND RAW MATERIALS MIXING
Raw materials, cement, water and admixtures are introduced and homogenized in the mixer.
Project Solid Life:
The same process is used to produce Solidia Concrete.







PRECAST PRODUCTS FORMATION (PRESS)
Back

PRECAST PRODUCTS FORMATION (PRESS)
Precast products are prepared in a press machine. The concrete is vibrated and packed in molds to create multiple pavers on a board. The boards are then stored on racks.
Project Solid Life:
The same process is used to produce Solidia precast products. Prior to carbonation, imperfect Solidia products can be broken up and recycled back into the mix to be reformed, reducing waste and saving money for precasters.







PRECAST PRODUCTS CURING
Back

PRECAST PRODUCTS CURING
Once prepared, the OPC precast products are cured in curing chambers at the specific temperature and humidity conditions needed to speed up strengthening and hardening. After a given time, they are taken out of the chamber.
Project Solid Life:
Solidia Cement only reacts with CO2, unlike OPC, which reacts with water. During the curing process, which uses the same temperature and humidity atmosphere as OPC, CO2 – from waste flue gas – reacts with Solidia Cement to form calcium carbonate. It is permanently transformed from a gas to a solid that resembles natural limestone. When the reduced CO2 emissions associated with Solidia Cement production are considered along with the ability of that cement to sequester CO2 during concrete curing, the carbon footprint associated with the manufacturing and use of cement can be reduced by up to 70% compared to OPC. This reduction is equal to 550 kg of CO2 per tonne of cement.







PRECAST PRODUCTS OUTSIDE STORAGE
Back

PRECAST PRODUCTS OUTSIDE STORAGE
OPC precast products can require many days to achieve full strength. Manufacturers store them during this process before they are sold and shipped.
Project Solid Life:
The CO2 curing process allows Solidia Concrete products to gain full strength in just 24 hours. Solidia’s precast products can be shipped immediately following the curing process, reducing the need for storage space and strengthening time, thereby saving manufacturers time and money.





